Navigating printing and coding solutions for next-generation flexible packaging
Flexible packaging plays a vital role in today’s supply chain, but its multi-material structure often makes it difficult, if not impossible, to recycle. As a result, many industries are shifting toward mono-material solutions that maintain packaging performance while improving recyclability.
Traditionally, films used for flexible packaging are made from several layers of material laminated together. Each layer consists of different materials chosen for their specific attributes, such as barrier properties, printability, and heat-sealing ability.
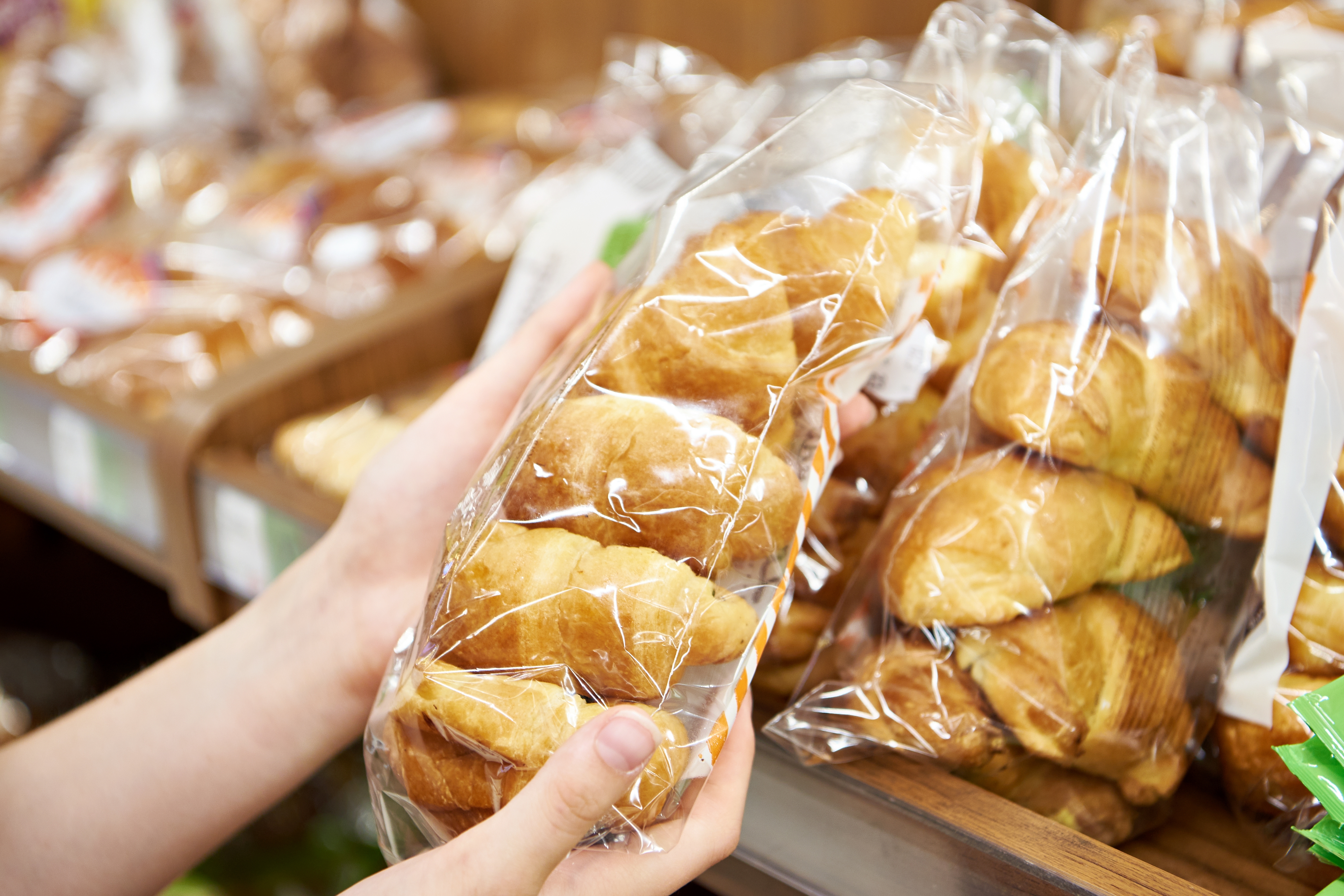
While this lamination of different materials can perform exceptionally well in packaging applications, it can make recycling difficult. There is often no economical way to separate the materials in the mechanical recycling process, so a lot of flexible packaging ends up in landfills.
As a result, brands are looking for options that will match the performance of traditional packaging materials while improving recyclability.
Stay ahead with real-time updates on the latest news:
What are mono-materials?
Replacing traditional multi-material laminated packaging with alternatives that offer enhanced potential for recyclability, such as mono-materials, is a growing solution for brands.
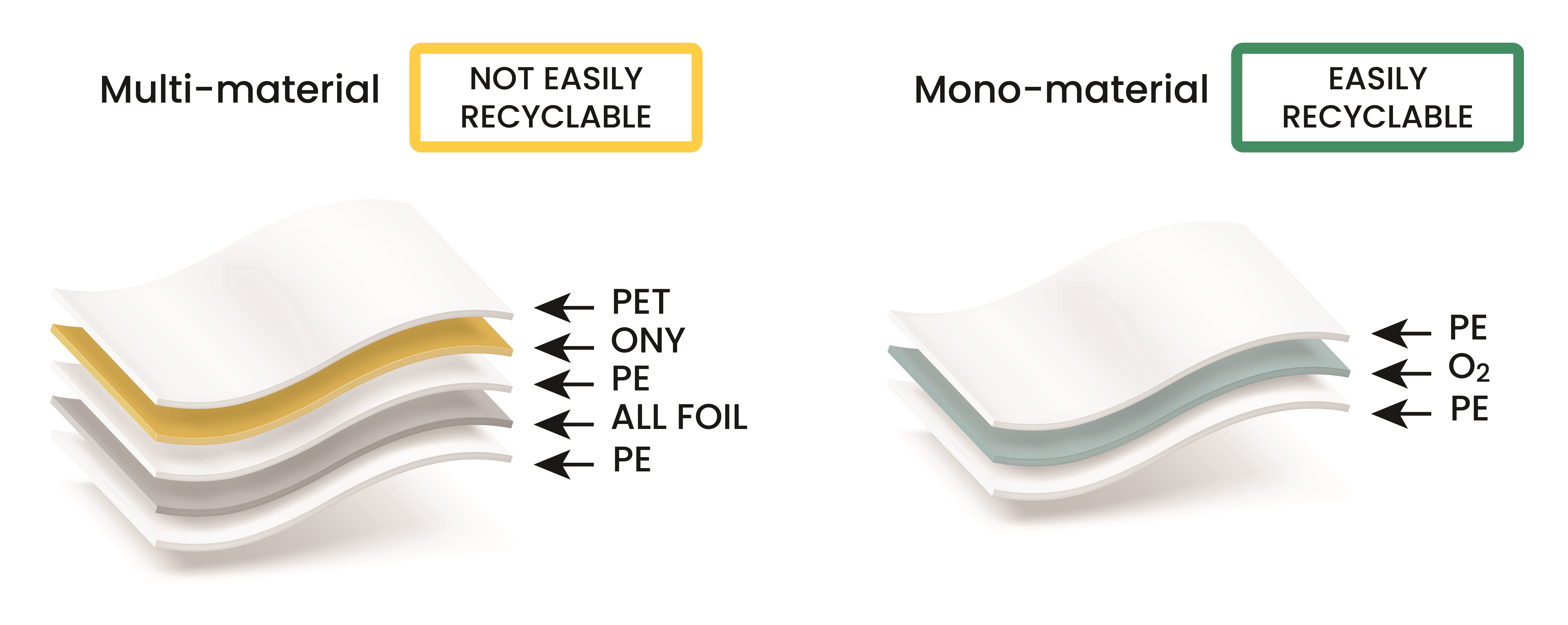
As the name suggests, a mono-material film replaces the mix of multiple components used in flexible packaging with just one type of material. The typical requirement to be considered mono-material is 90% of the same material by weight.
Paper, aluminum, and plastics like polyethylene (PE), polypropylene (PP), and polyethylene terephthalate (PET) are examples of mono-materials that can help with recycling. However, this is not without some challenges.
Performance challenges
Transitioning from traditional film packaging to a single-material solution poses some performance obstacles, such as decreased barrier properties when moving from PET or aluminum-layered material to PE. Yet it’s often possible to enhance mono-material packaging with barrier coatings. These coatings, which safeguard against moisture, oxygen, and UV light, are applied to preserve the product’s integrity and prolong its shelf life. Importantly, producers can ensure that the integration of these protective coatings is designed to harmonize with the recycling process.
Printing and coding challenges
When switching to a mono-material for flexible packaging, all package printing, including the variable information added for date/lot codes and barcodes, needs to be considered.
Mono-materials possess lower surface energy (the property that determines how well ink or adhesive adheres to its surface) than traditional flexible packaging materials. This change in surface energy may require an alternative printing ink that has better adhesion performance.
When using a laser marking system, adjustments may be required to accommodate mono-materials, which are typically thinner than conventional multi-materials. These adjustments can vary from straightforward changes in settings to potentially selecting an alternative laser system that more effectively interacts with the material.
Improving printability on mono-materials
Fortunately, there are solutions that allow for successful printing onto mono-material packaging, both at the packaging converter’s plant and on the packaging line.
Before the primary printing is carried out during the converting process, the surface to be printed can be coated with a very thin aqueous-based primer that is receptive to flexographic and digital printing. The coating does not affect the recycling process and can be applied by the film manufacturer or as part of a printing system.
As an alternative, the material’s surface can be enhanced using a corona or plasma system by the film manufacturer or at the time of printing. These systems increase the material’s surface energy, enabling printing to take place.
On the packaging line, the placement of the coding solution, environmental conditions, and the coding technology itself will all factor into providing the right code quality and adhesion. Laser codes are permanent, while ink-based solutions offer specially designed inks with key performance traits, such as durability on flexible films and glossy substrates.
How to code on mono-materials
Fortunately, today’s primary packaging coding systems work well with flexible packaging substrates, including mono-materials. Your coding partner can help you find a solution that will meet your requirements for the new, more sustainable packaging and address any change in porosity or surface energy.
In many cases, a simple change of ink or printing ribbon might be all that is required, depending on the type of coding technology in use. For example:
- Continuous inkjet (CIJ) printers: With hundreds of inks engineered for compatibility with many different packaging substrates, identifying the ideal ink for your new mono-material application should involve testing and working closely with a coding and marking expert. To get the best print result, you might need to replace your ink with one more suitable for a lower surface energy packaging material.
- Thermal inkjet (TIJ) printers: Again, with a wide portfolio of ink types available, testing may be needed to identify the right ink to print on a new mono-material.
- Thermal transfer overprinters (TTO): When switching to a mono-material, it is likely that a change to the print darkness, force, and speed parameters, and perhaps changing to a ribbon with higher resin content, may be needed.
- Laser marking systems: Lasers of certain laser wavelengths, like UV lasers, are particularly well-suited for marking on flexible films including mono-materials. The Videojet 7920 UV laser, for instance, performs well on various mono-material films. Testing should be performed with your new materials to ensure compatibility.
Note that when changing to mono-material packaging, there are usually some changes needed to the parent packaging machine to be sure it will handle the new material successfully. This includes ensuring that the package seals are still produced correctly, and the new material runs through the process properly.
As part of this process, it should be confirmed that the registration accuracy of the packages on the machine hasn’t been compromised, and the printed codes will always be in the correct location.
Achieving quality printed codes on mono-material packaging
When switching from traditional flexible packaging to a more sustainable mono-material solution, it is essential that the product coding is considered, along with any packaging machine upgrades.
Drawing on our vast experience in applying high-quality date and product codes, such as GS1 Sunrise 2027 2D codes, across a range of packaging materials, Videojet stands ready to support the successful introduction of your sustainable packaging initiatives.
Additional reading:
Videojet: The Rise of Mono-Materials: Balancing Sustainability with Performance in Packaging
Videojet: Sunrise 2027: 2D Code Revolution
Videojet: Printing Barcodes and 2D Codes